Technics: MIM
Quoted Condition: 2D / 3D Drawing / Sample
Package: Carton, Plastic Bag, Export Package
OEM/ODM: Welcome
Precision Processing: Mixing, Injection, De-Binding, Sintering
Production Time: 15-30 Days
Weight: 14.8g
Size: 10.5*10.4 mm
Trademark: drome
Transport Package: Carton
Specification: 290*190
Origin: Suzhou, China
Metal Injection Molding (MIM) is the fifth generation of metal forming technology. Over the past four decades, it has evolved significantly and found widespread application, especially in the 3C industry. From early exploration to a mature stage, MIM has played a crucial role in the development of 3C products. Several key components such as hinges, fiber optic connector bases, and new-style connectors are heavily reliant on MIM technology. These parts are now produced in large quantities, and MIM is being increasingly adopted across industries.
At Drome, we provide comprehensive one-stop solutions for both MIM and CIM technologies. Our services include:
1. Economical production of complex parts ranging from 0.03g to 200g using high-performance engineering materials.
2. Parts with high dimensional accuracy (±0.1%~±0.5%) and excellent surface quality (surface roughness 1~2μm).
3. High relative density (96%~100%), homogeneous microstructure, and superior mechanical performance.
4. Flexibility in material selection, supporting various powders and broad application scope.
5. Efficient resource use through waste recycling, automated production, and suitability for mass production.
The MIM process involves several key steps: mixing, injection molding, de-binding, and sintering. This allows for the creation of intricate and high-quality metal parts that meet strict industrial standards.
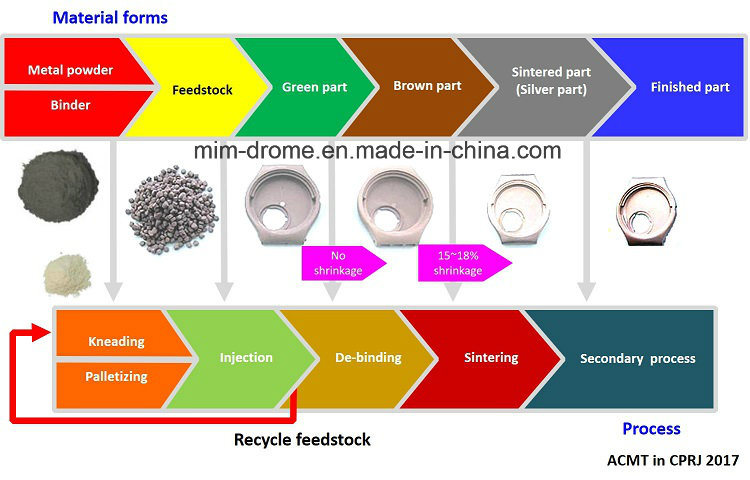
MIM technology is widely used in various applications, including but not limited to rotating shuttle parts, sewing machine components, and more. Below is a visual representation of its usage:
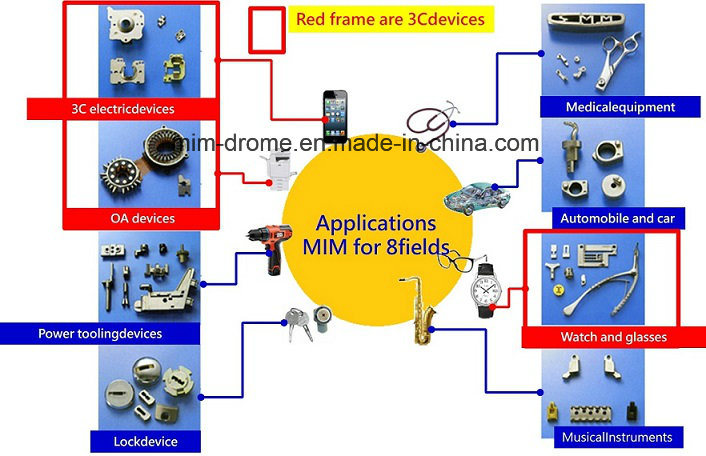
**Product Range:**
| Material | Density (g/cm³) | Tensile Strength (MPa) | Yield Strength (MPa) | Elongation (%) | Young's Modulus (GPa) | Impact Energy (J) | Hardness (Rockwell) |
|------------------|------------------|--------------------------|-----------------------|----------------|------------------------|--------------------|----------------------|
| MIM-Fe2Ni | 7.8 | 280 | 115 | 25 | - | - | 55 HRB / 50 HRC |
| MIM-Fe8Ni | 7.8 | 450 | - | 12 | - | - | 84 HRB / 50 HRC |
| MIM-2200 (as sintered) | 7.8 | 290 | 125 | 40.0 | 190 | 135 | 45 HRB |
| MIM-2700 (as sintered) | 7.8 | 415 | 255 | 26.0 | 190 | 175 | 69 HRB |
| MIM-4605 (as sintered) | 7.8 | 440 | 205 | 15.0 | 200 | 70 | 62 HRB |
| MIM-4605 (Q&T) | 7.8 | 1655 | 1480 | 2.0 | 205 | 55 | 48 HRC / 55 HRC |
| MIM-304L | 7.8 | 500 | - | 70 | - | - | 60 HRB |
| MIM-316L (as sintered) | 7.85 | 520 | 175 | 50.0 | 190 | 190 | 67 HRB |
| MIM-410 | 7.7 | 900 | - | 7 | - | - | 40 HRC |
| MIM-420 (heat treated) | 7.7 | 1380 | 1200 | 12 | 190 | 40 | - / 45-60 HRC |
| MIM-430L (as sintered) | 7.8 | 410 | 240 | 25.0 | 210 | 150 | 65 HRB |
| MIM-440C | 7.8 | 700 | 590 | 15 | - | - | - / 45-60 HRC |
| MIM-17-4PH (as sintered) | 7.8 | 900 | 730 | 6.0 | 190 | 140 | 27 HRC |
| MIM-17-4PH (heat treated) | 7.8 | 1190 | 1090 | 6.0 | 190 | 140 | 33 HRC / 40 HRC |
**Material Properties Table:**
| Material | Density (g/cm³) | Tensile Strength (MPa) | Elastic Modulus (GPa) | Thermal Conductivity (W/m·K) | Thermal Expansion (×10â»â¶/K) |
|------------------------|------------------|--------------------------|------------------------|------------------------------|------------------------------|
| Copper (Cu) | 8.9 | 100 | 130 | 250 | 13 |
| Invar (Fe-36Ni) | 8.0 | 300 | 205 | 20 | 5 |
| Kovar or F15 (Fe-29Ni-17Co) | 8.0 | 480 | 200 | 17 | 4.9 |
| Molybdenum-Copper (Mo-15Cu) | 10.0 | 210 | 280 | 170 | 7 |
| Molybdenum-Copper (Mo-20Cu) | 9.9 | 200 | 280 | 145 | 6.5 |
| Tungsten-Copper (W-10Cu) | 17.0 | 500 | 340 | 209 | 6 |
| Tungsten-Copper (W-20Cu) | 16.0 | 560 | 290 | 247 | 7 |
| Tungsten-Copper (W-30Cu) | 14.0 | 420 | 260 | 260 | 11 |
**Application Fields:**
| Industry | Examples |
|--------------------|--------------------------------------------------------------------------|
| Aerospace | Airfoil Hinge, Rocket Nozzle, Guided Missile Spoiler, Turbine Blade Core |
| Auto Industry | Ignition Control Lock Parts, Turbo Charger Rotor, Valve Guide Rail, Brake Gear Parts |
| Electronics | Disc Drive Parts, Cable Connector, Electronic Valve Shell, Heat Sink Material |
| Defense Industry | Mine Rotor, Gun Trigger, Armor Piercer, Sight Base |
| Medical Industry | Orthopaedic Bracket, Internal Sewing Needle, Biopsy Forceps |
| Daily Necessities | Watch Shell, Golf Head, Sport Shoe Buckle, Hole Puncher |
| Mechanical Industry| Irregular Milling Cutter, Micro Gears, Sewing Machine Parts |
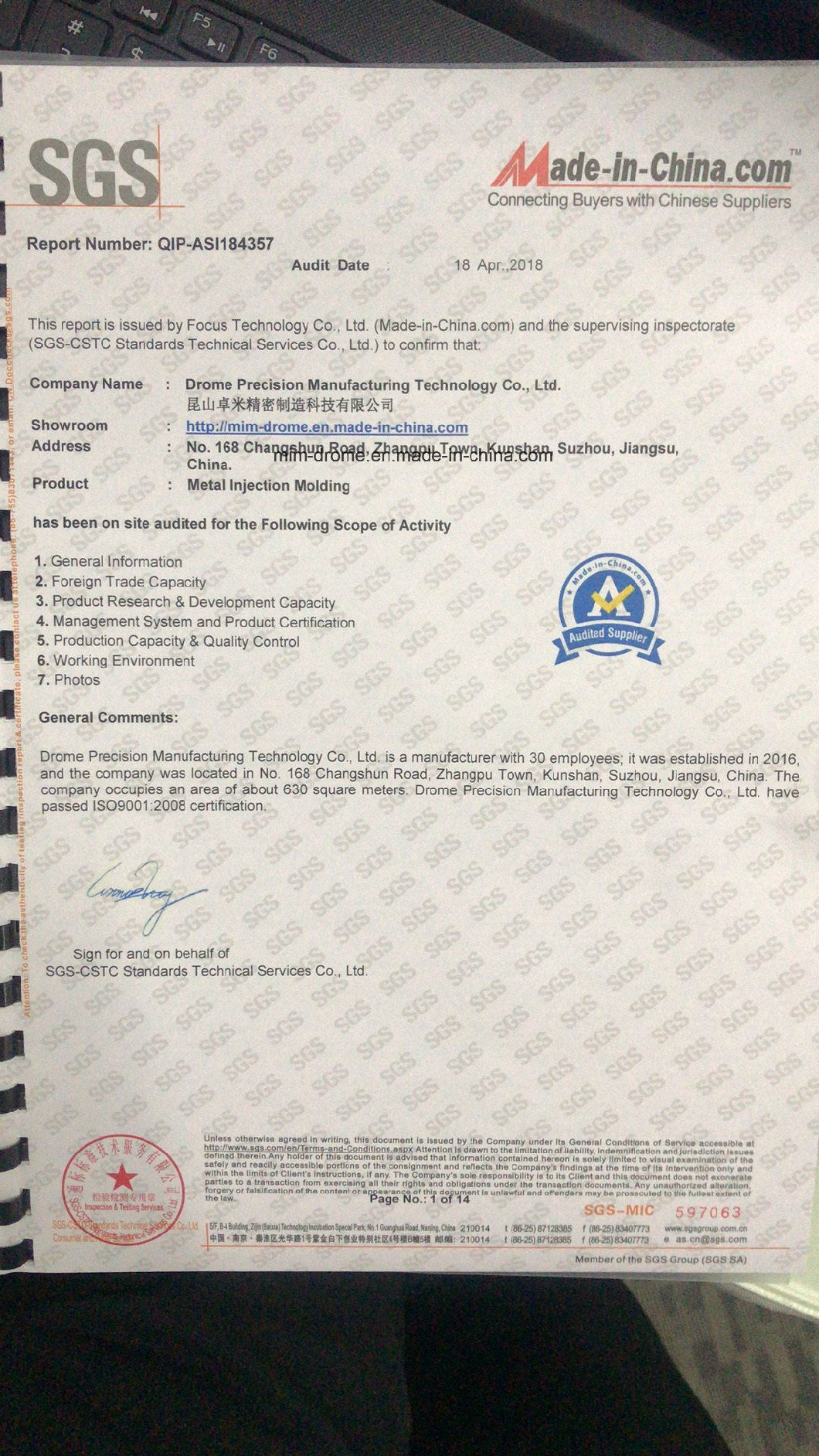
**FAQ:**
1. **How can I get a quote?**
Please send us your 2D/3D drawings. The process includes:
Customer Inquiry → Engineering Communication → Cost Analysis → Sales Analysis → Quote to Customer.
It typically takes 1 work day.
2. **How do you ship the product?**
For small quantities, we use TNT, FEDEX, UPS, etc. For large orders, air or sea shipping is available.
3. **What about packaging?**
We normally use plastic bags or cartons. If the customer has specific requirements, we will follow them.
**Company Profile:**
- Design and manufacture Metal Injection Molding (MIM), Ceramic Injection Molding (CIM), and Plastic Injection Molding (PIM) parts.
- 10,000 sq.m of manufacturing space, with 30,000 sq.m under construction.
- Over 200 employees, including 17 engineers.
- Annual sales revenue exceeded $10 million in 2017.
- Certified with IATF 16949, ISO 9001, OHSAS 18001, and ISO 14001.
- Invest 5% of annual revenue into R&D.
- Equipped with advanced machinery from Germany (Arburg), Japan (Nissei, Shimadzu), etc.
- Serving top companies in the automotive, consumer electronics, and medical industries.
Extruder maintenance equipment
Ensuring the feed screw and barrel remain in top condition is an essential part to achieving processing goals. Over time and under continuous operating conditions, the feed screw and barrel will experience wear. You will need both cleaning tools and measuring tools to ensure accuracy of your measurements. PromaXX provides Maintenance Equipment to our valuable customers in the daily maintenance of Feed screw and Barrel.
Equipment,Extruder Equipment,Extruder Screw,Twin Screw Extruder Machine
Jiangmen PromaXX Extrusion Technology Co.,Ltd. , https://www.extruder-service.com