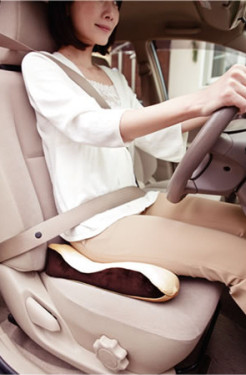
Nowadays, cars are gradually changing our lives, but while bringing convenience to us, some unhealthy habits also unknowingly recruit us. According to research, more than 2 hours of driving, lumbar injuries have already occurred. Among them, the principle is that one does not move for a long time, the muscles of the lumbar spine are tense, and the second is the ups and downs, the bumps and vibrations, and the destruction of the intervertebral disc.
So it is recommended to have car owners:
1, a drive time should not be too long, or physical and mental fatigue, not only affect the safety of driving but also endanger the health. During the driving process, it is generally possible to park and rest every 2 hours. This can help the muscles to eliminate fatigue and provide a healing effect, thereby reducing the damage caused by the vibration. This intermittent rest can also alleviate other damages caused by noise in driving and bad weather conditions. In the face of poor road conditions, the speed can not be too fast, the operation should not be too fierce, or the car's severe bump on the lumbar spinal injury.
2. Reduce the vibration of the car, make pre-judgment and smooth driving ahead of the road conditions, which can not only improve driving safety, but also reduce the load on the waist.
"Gravity Die Casting. A permanent mould casting process, where the molten metal is poured from a vessle of ladle into the mould, and cavity fills with no force other than gravity, in a similar manner to the production of sand castings, although filling cn be controlled by tilting the die."
Sometimes referred to as Permanent Mould, GDC is a repeatable casting process used for non-ferrous alloy parts, typically aluminium, Zinc and Copper Base alloys.
The process differs from HPDC in that Gravity- rather than high pressure- is used to fill the mould with the liquid alloy.
GDC is suited to medium to high volumes products and typically parts are of a heavier sections than HPDC, but thinner sections than sand casting.
Gravity Casting Parts,Aluminum Alloy Gravity Casting Parts,Aluminum Gravity Die Casting Parts,Gravity Casting Aluminum Parts